Accelerating the Design of a Castable Gearbox Housing for a Hybrid Vehicle
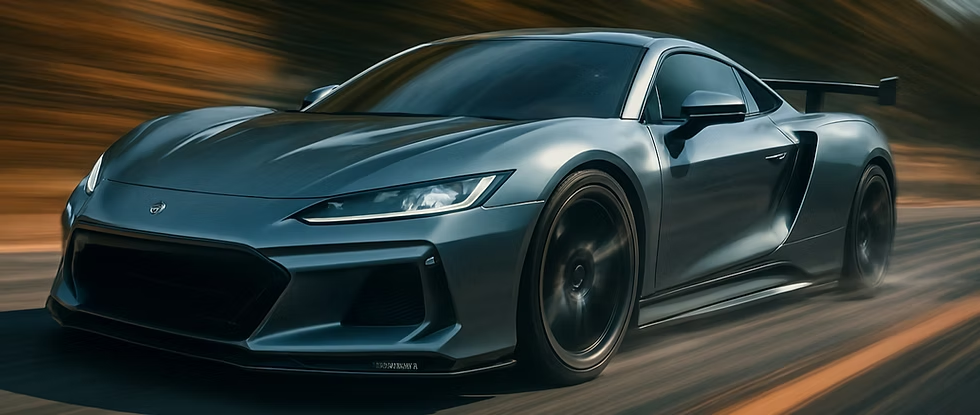
Gearbox housings remain as one of the car components that must now respond to continuous system evolution: changes in electric motor packaging, inverter positioning, new cooling layouts, shifting loadpaths... Design engineers are on the front line, responsible for delivering parts that fit evolving assemblies, meet performance targets, and comply with casting-specific manufacturing rules. However, fragmented workflows and rigid CAD processes make this task time-consuming and error-prone.
This case study focuses on the design of a castable gearbox housing for a next-generation hybrid vehicle, showing how the integration of performance and manufacturability constraints within an automated workflow allows engineers to deliver more reliable, and production-ready results 10 times faster, even when system definitions change mid-stream.
The optimized part
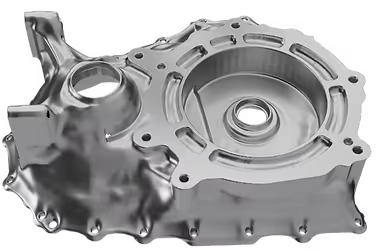
The outcomes
Engineering lead time reduction:
10 times faster (from 5 days to 12 hours) than conventional casting design workflow.
Interested in reading the full case study?
Fill in the form below to instantly receive the full case study.
Aeronautics Challenges We Address
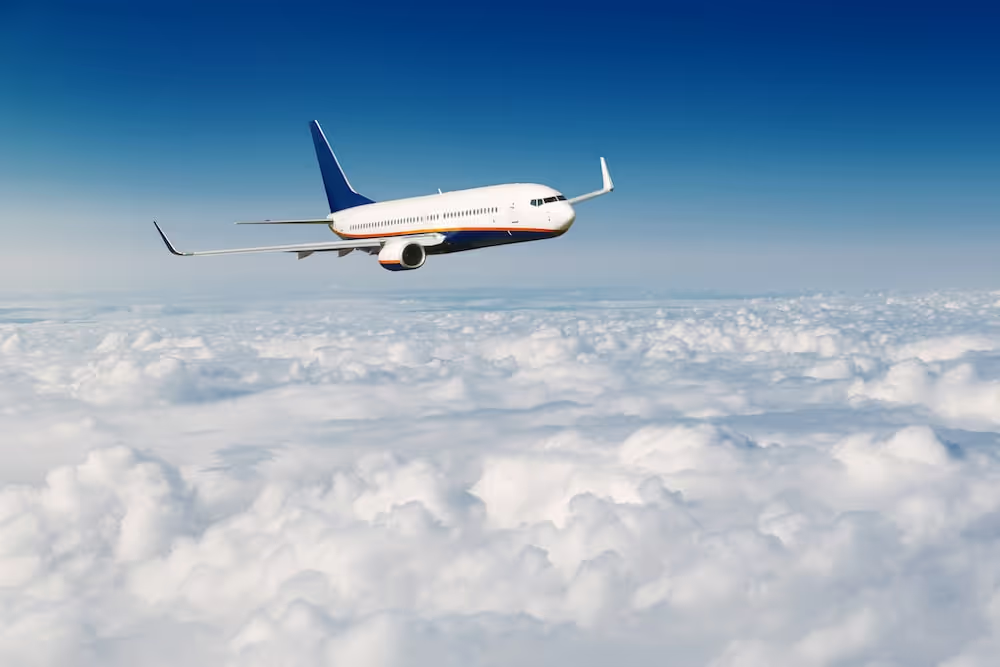
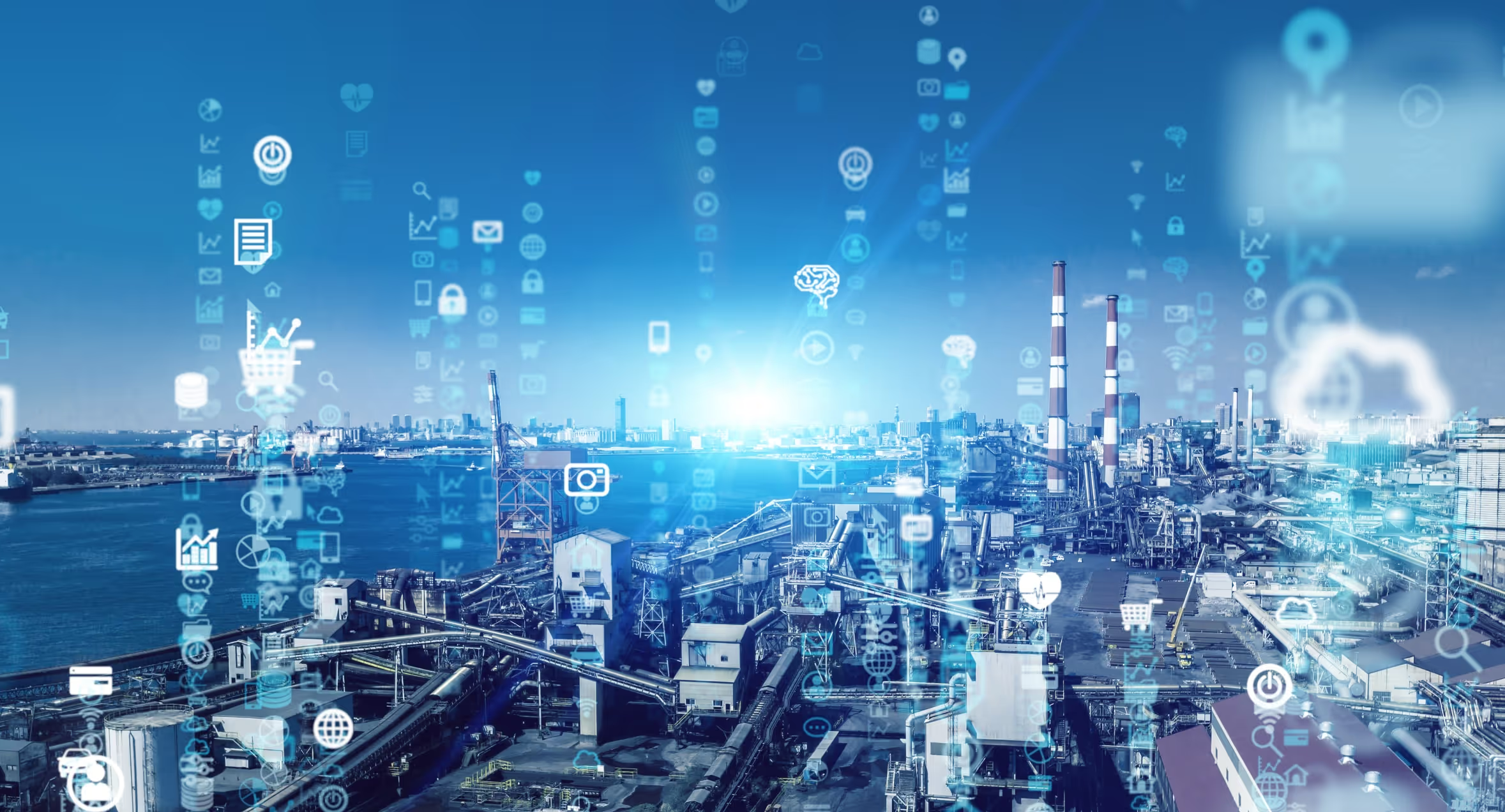
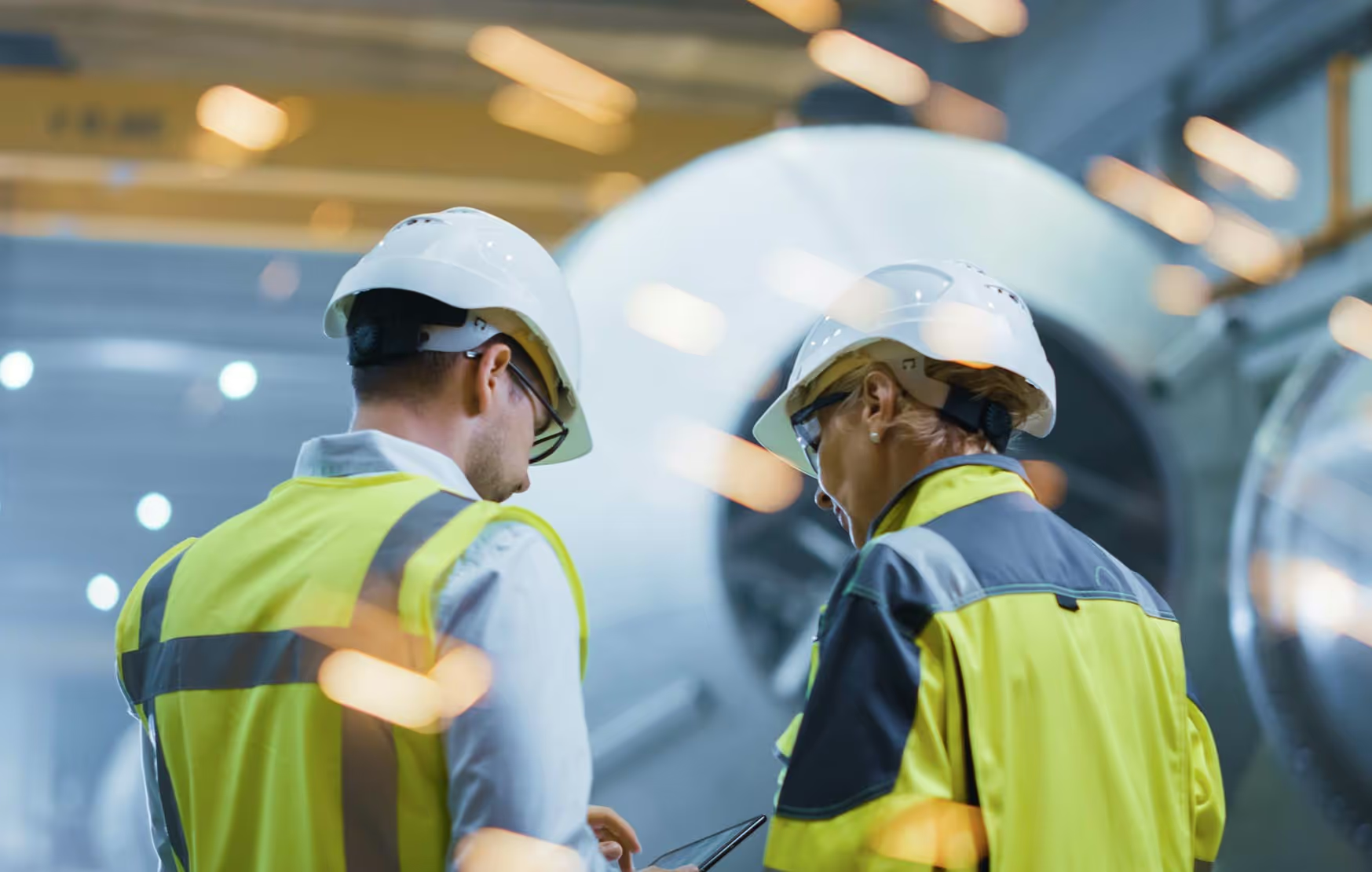
Automotive Challenges We Address
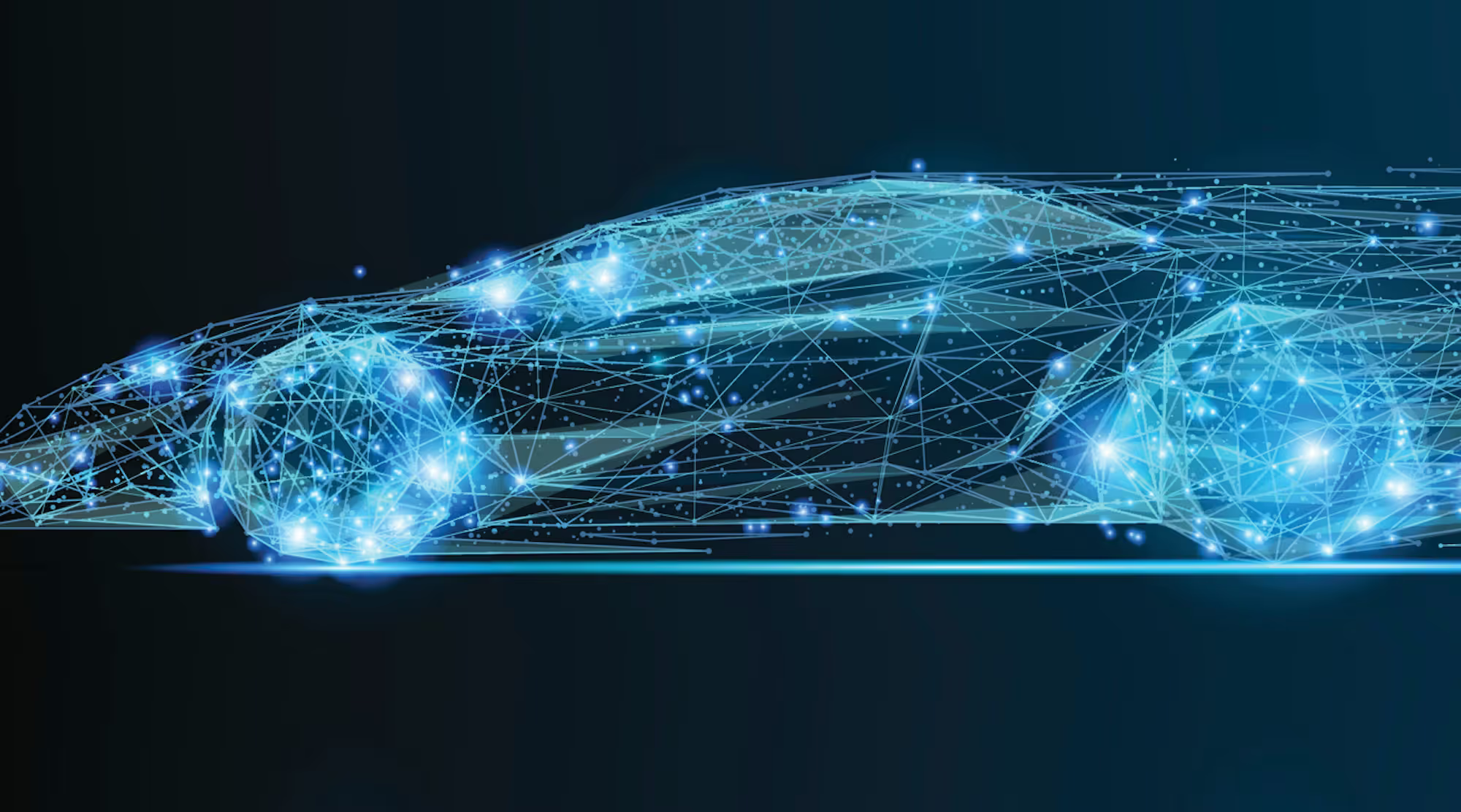
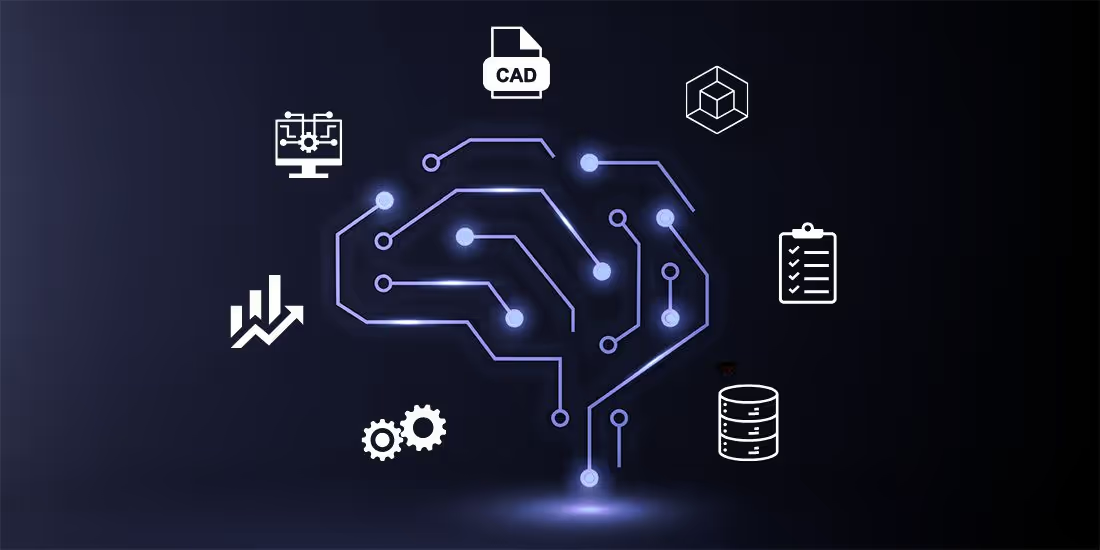
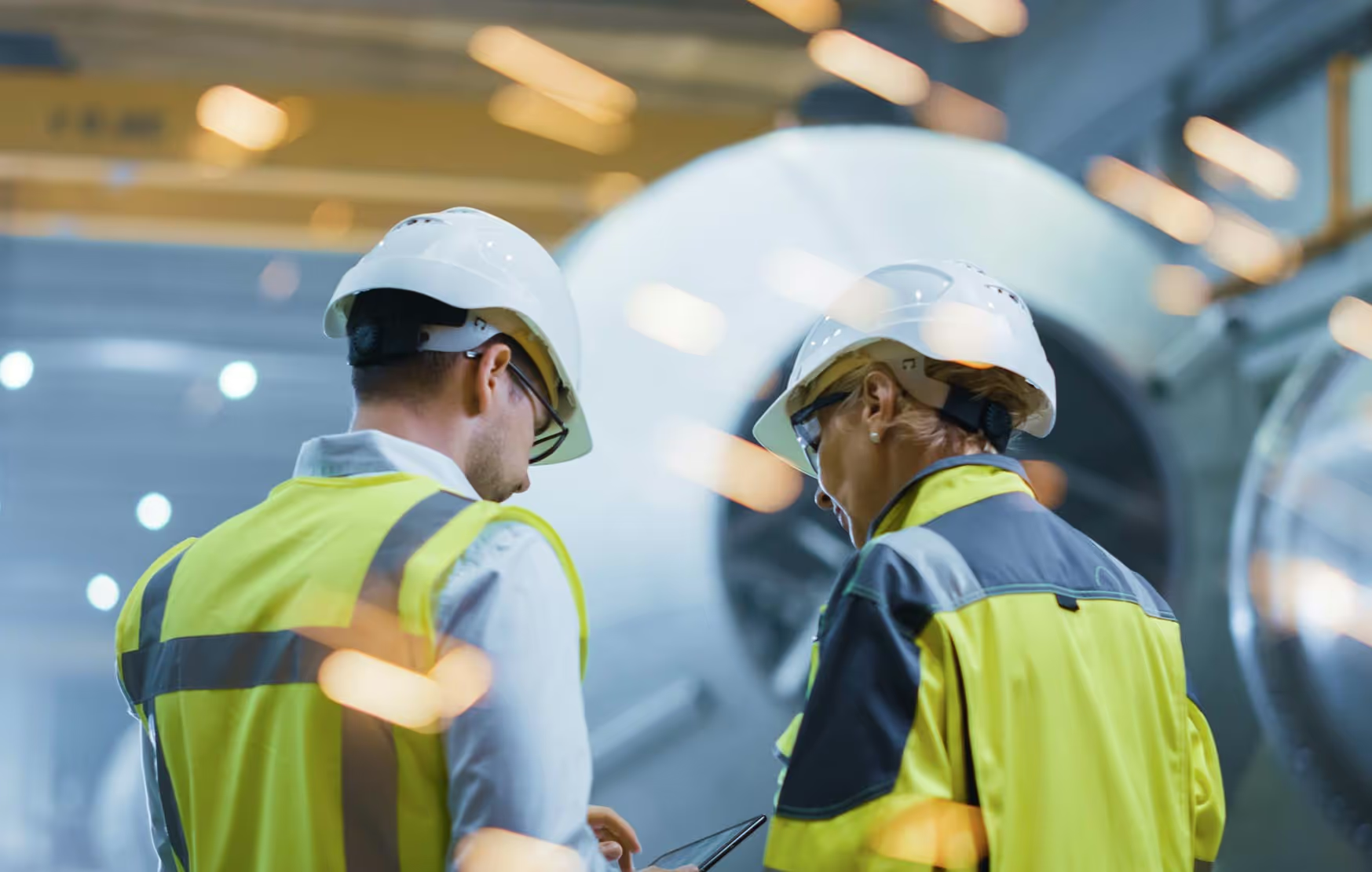
Defense Challenges We Address
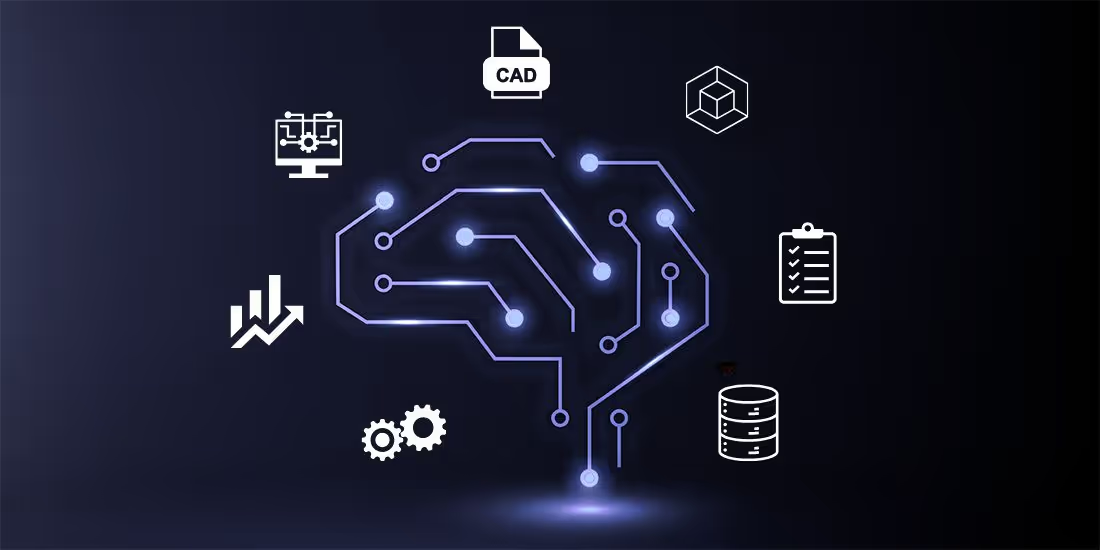
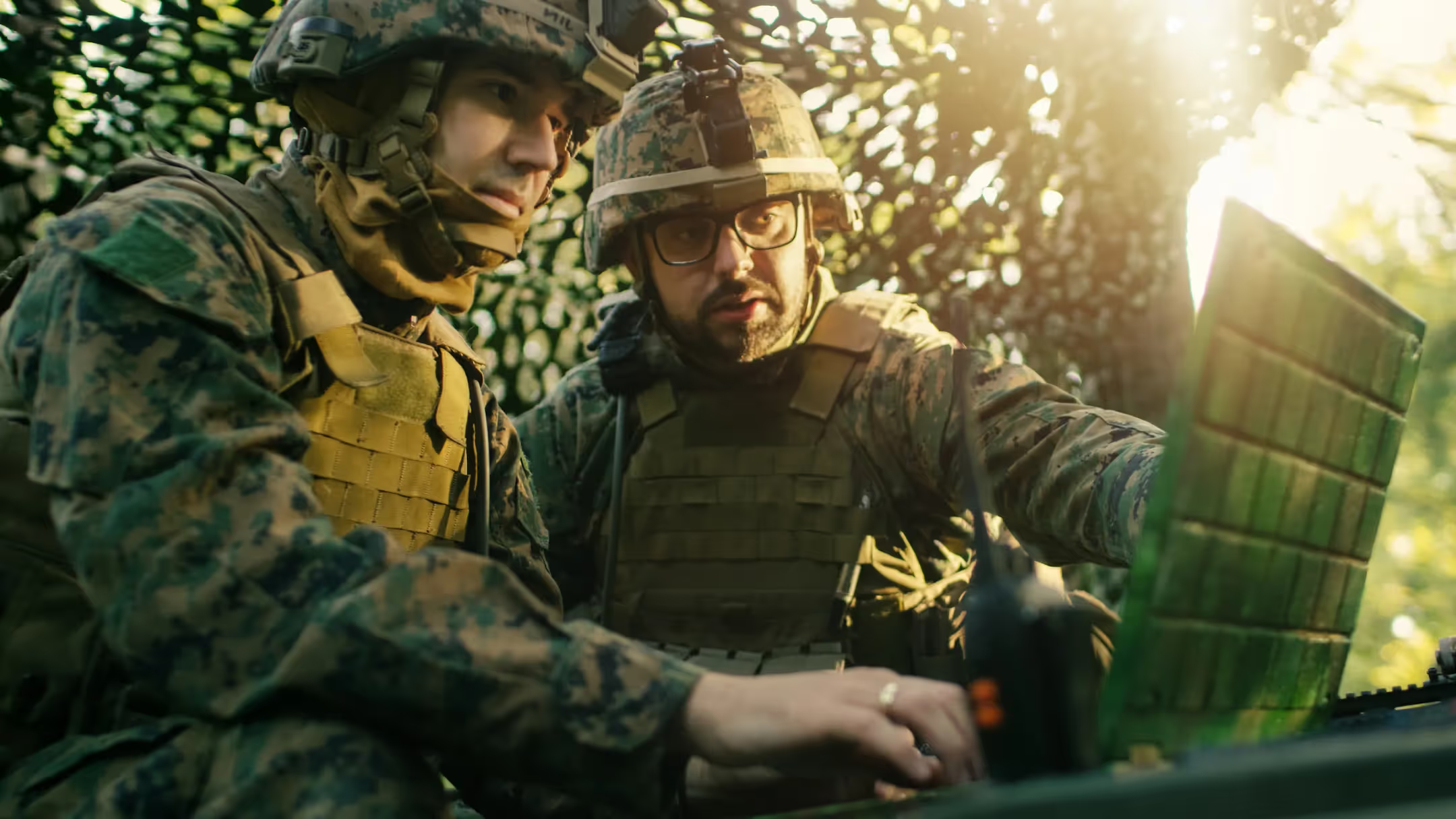
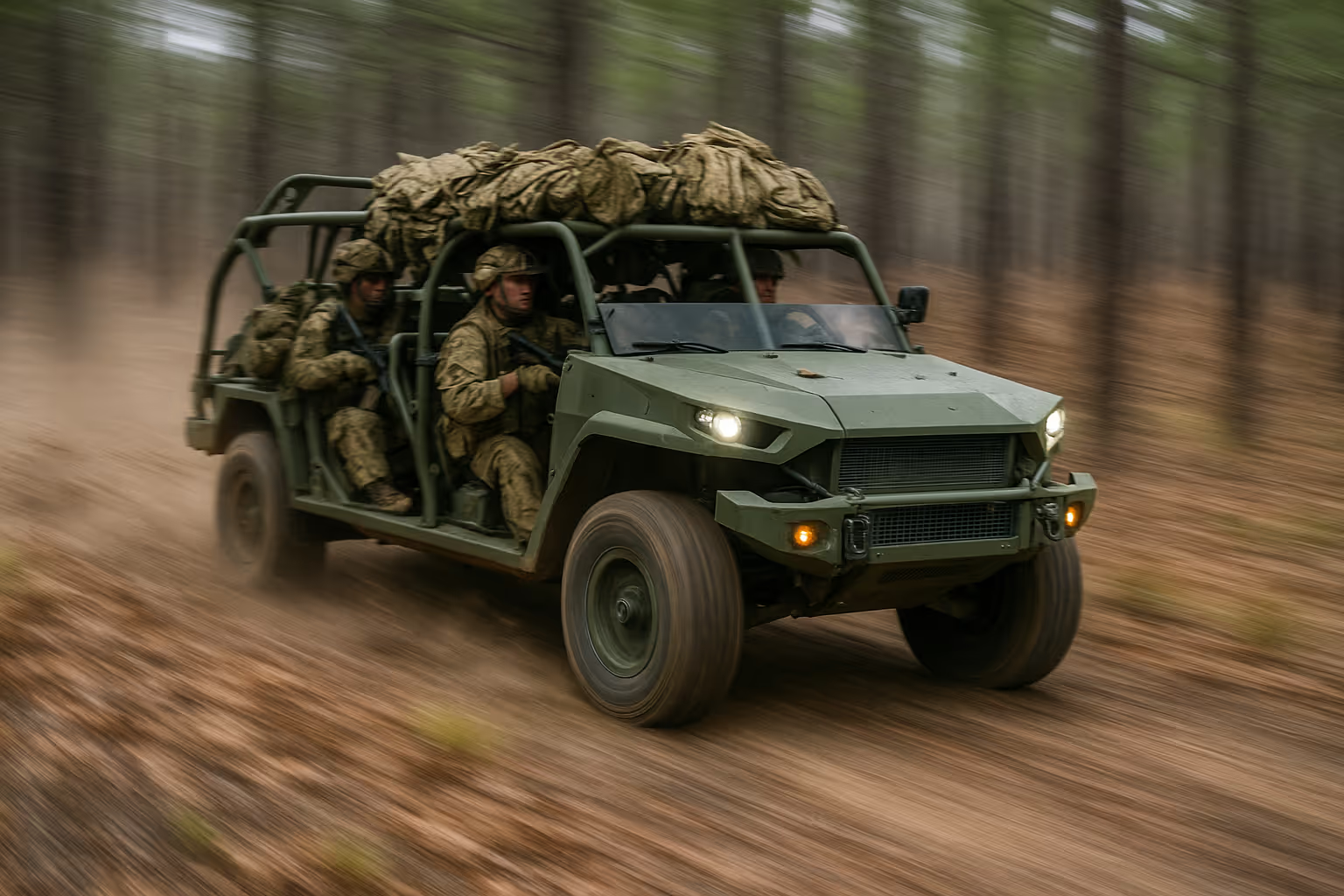
Built for the Cognitive Era of Engineering
Shorten product development cycle from the earliest concept phase.
Product engineering cycle
Product engineering cycle
Reusability of engineering workflows
FAQs
Explore our frequently asked questions to understand how our software can benefit you.
Yes, some functions in Cognitive Design by CDS use AI (costing, conversion to CAD, manufacturing analysis). It is pre-trained by CDS and packaged in the software, so there is no training happening on your side, and your data is not used.
Yes, you can convert mesh or implicit models to CAD and export them as a .step. It works best for midly complex models (e.g. generative design results). Complexe models (integrating lattice structures for instance) can also be converted to CAD, but would take more time..
No, our workflows use hybrid meshing, keeping the original CAD precision around functional regions, and having smooth mesh elements on organic features.
Cognitive Design by CDS uses a proprietary hybrid geometrical engine, mainly based on implicit modeling (Signed Distance functions), with in addition mesh and CAD operators.
Cognitive Design by CDS uses a node-locked license system, tied to each workstation. This approach aligns with the offline, on-premise setup. Floating licenses are not yet available.
Cognitive Design by CDS is particularly well suited for complex, high-value mechanical parts such as lightweight structures, gearbox housings, functional brackets, or fixtures subjected to multiphysics loads. It is optimized for use cases in aerospace, defense, space, and advanced mobility systems.
Cognitive Design by CDS is an advanced concurrent plaftorm for design optimization that enhances component performance. It incorporates production constraints directly into the design phase, ensuring efficiency. This allows design engineers to streamline workflows and reduce development time.
Cognitive Design by CDS is tailored for engineers in large and medium-sized industrial companies. It is particularly beneficial for sectors like aerospace, automotive, defense, and space. The software addresses unique engineering challenges faced in these industries.
Cognitive Design by CDS uses an implicit modeling engine and parametric design to generate and optimize designs rapidly. By factoring in manufacturing constraints, it ensures that designs are feasible and efficient. This process minimizes the risk of failure during production.
Cognitive Design by CDS significantly reduces development time and enhances agility in the design process. It allows for quick iterations and optimizations, keeping your projects on track. By integrating manufacturing constraints early, it helps maintain competitiveness.
While Cognitive Design by CDS is user-friendly, we offer comprehensive training to maximize its potential. Our support team is available to assist with onboarding and any questions. This ensures that users can leverage the software effectively.
Unlock Your Design Potential
Request a demo to see how Cognitive Design by CDS can revolutionize your engineering workflow