How Cognitive Design Blasted Away the ULA Grabcad Challenge: A Practical Case Study of Part Optimization
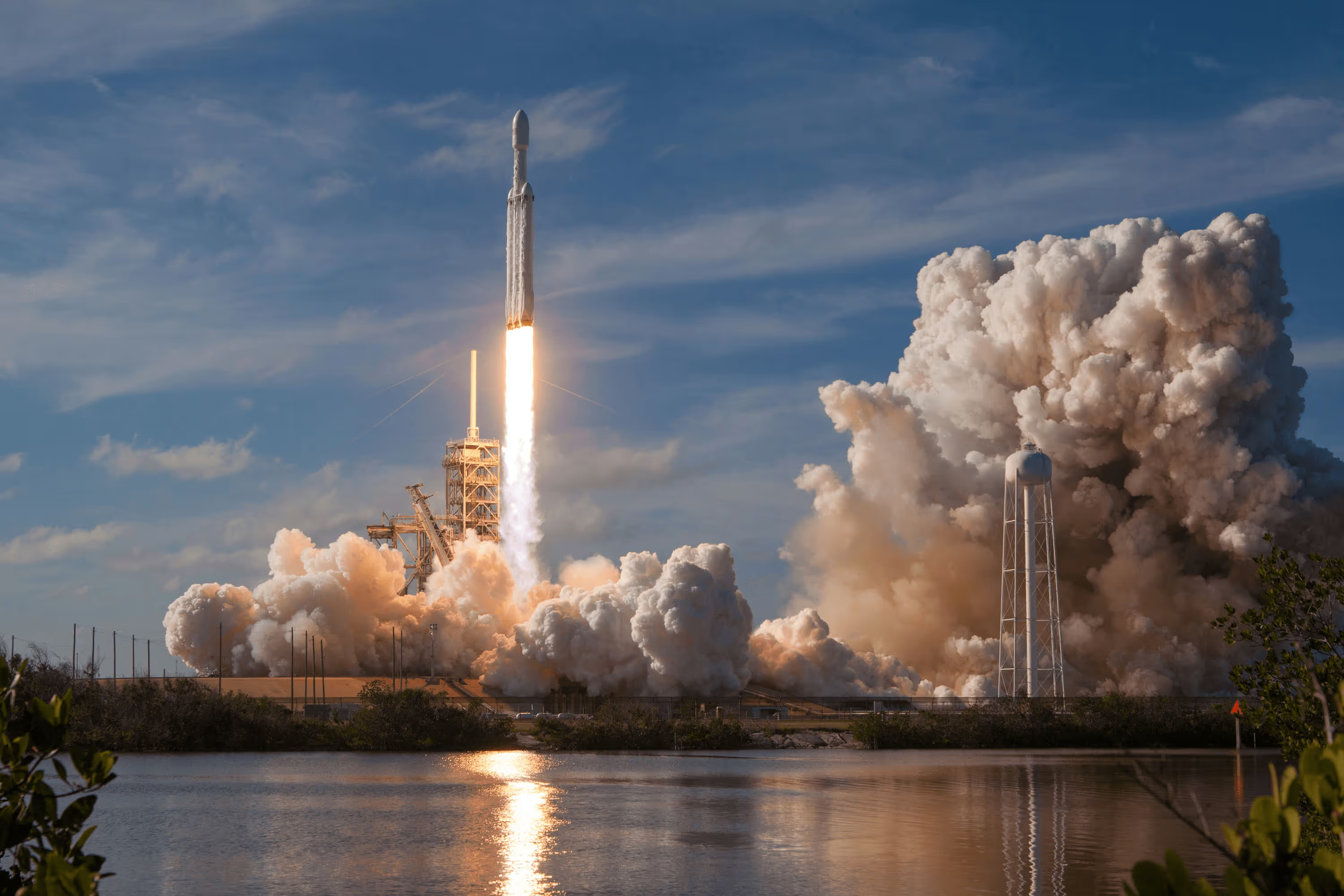
This article highlights how, with Cognitive Design, we achieved significantly better performance than the first-prize-winning design in the ULA Grabcad Challenge, where top engineers competed to create a component that met stringent criteria for weight and strength. By leveraging advanced tools like topology optimization post-processing application and the simulation-driven design (SDD) approach, Cognitive Design was able to deliver a design that was lighter, stronger, in a more effective manner.
If you're curious about how automation and simulation can revolutionize your overall design process, this article practically outlines how, with Cognitive Design, you can effortlessly push current engineering boundaries even further.
The ULA Grabcad Challenge: Context and Frame
The Grabcad Challenge is a global engineering platform where top engineers compete against each other on multiple contests for various industries and purposes. In our case, the objective of this challenge was to create a launch support bracket for ULA (United Launch Alliance) rockets that was not only lightweight and strong but also easy to mount with precise load specifications.
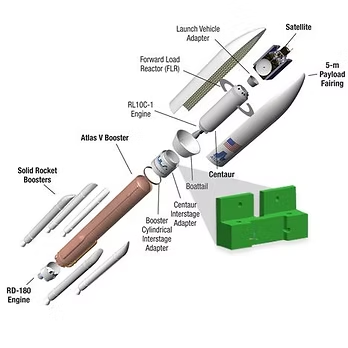
Participants in the challenge had to face several critical design constraints:
- Weight Limits: Maximum 45,4 grams.
- Material Selection: Ultem 9085
- Load to withstand: 2,7 kN
- Size and Geometry Constraints: The part had to fit within predefined spatial limits (design space), as shown in the picture below.
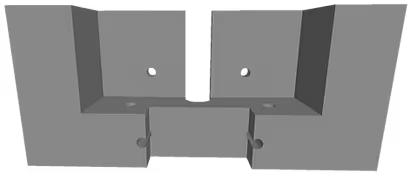
Find more information about the ULA GrabCAD Challenge here.
Presentation of the First-Prize-Winning Design
The first-prize winner of the ULA Grabcad Challenge set a high bar, achieving impressive performance results. The design showcased significant advancements in weight reduction, stress management, and load-bearing capacity, while adhering to the stringent specifications outlined in the challenge.
Here’s a breakdown of the key performance metrics they achieved:
- Weight: 40.7 grams
- Volume: 329.9 cm³
- Maximum Stress: 33 MPa
- Design Time: 50 hours
- Estimated Labor Cost: $5,000 (50 hours x $100 per hour)
- Load to Withstand: 2.7 kN
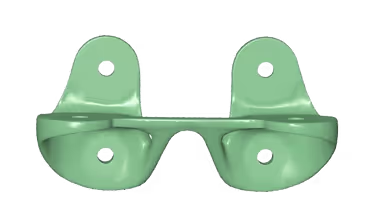
How Cognitive Design Took Up the ULA GrabCAD Challenge
In order to obtain the highest performance possible, we decided to leverage two of the most valuable capabilities of Cognitive Design. The first one is the automation of the topology optimization post-processing: Topology Optimization Post-Process app that, from raw results of topology optimization, reshapes the input design to obtain a smooth and flawless model, ready to be produced or modified. Once the post-processing of the topology optimization results is done, we combined it with the Simulation-Driven Design (SDD) app for further performance achievement through intelligent material redistribution in the part. Therefore, engineers are not limited to the topology optimization anymore but rather continue to fine-tune their designs with precision, eliminating manual iterations and ensuring optimal results.
Methodology
Here’s a simplified breakdown of how Cognitive Design was able to improve upon the winning solution:
Step 1: Topology Optimization Post-Process
The first step involved importing the design space and raw topology optimization results into the TO Post-Process app. This app excels at reconstructing and smoothly reconnecting broken geometries resulting from raw topology optimization, ensuring a cohesive design. It intelligently cleans up small entities, such as disconnected islands and mesh artifacts, refining your part to perfection. Using Boolean operations, it integrates functional regions seamlessly with the main design, smoothing sharp intersections and eliminating unwanted irregularities.
This automated approach not only enhances performance and manufacturability but also saves valuable time.
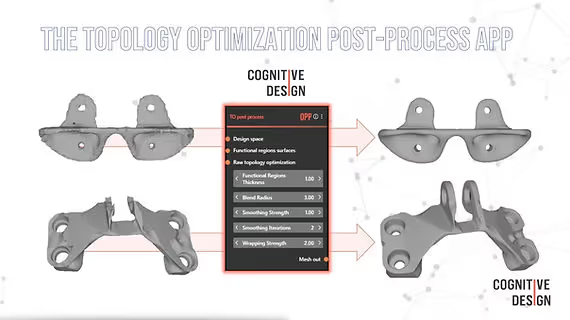
Step 2: Simulation-Driven Design app
Once the topology optimization was refined, we applied the Simulation-Driven Design (SDD) app based on the SDD approach to further enhance material distribution. This app uses stress analysis and simulation inputs to determine which areas of the part could afford material removal without compromising structural integrity.
By focusing on critical areas where constraints, loads, pressures, or temperatures are most significant, The SDD app offers advanced capabilities to optimize material distribution across the entire volume of a part, ensuring optimal performance with minimal mass.
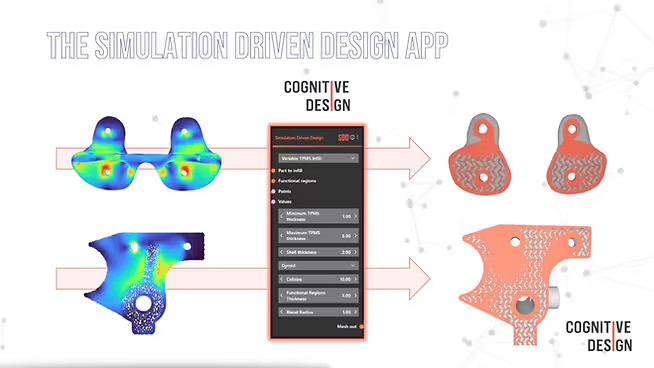
Multiple strategies are available in Cognitive Design to achieve the best optimization results, such as variable offset, shell, ribbing, and lattice/TPMS infill. In our case, we opted for the Variable TPMS Infill method to remove material in unconstrained areas. Then, we tweaked the geometrical parameters and chose a gyroid structure.
At each step of the optimization process, validation simulations were conducted to ensure that the design could withstand the loads specified in the ULA Grabcad Challenge. This verification was crucial in ensuring that the part met both performance and safety standards.
For a detailed breakdown of the entire workflow, watch the full video.
Cognitive Design vs. the First-Prize Winner – A Direct Comparison of Key Performance Metrics
When comparing the first-prize-winning design with our optimized solution, Cognitive Design not only matched the original design’s performance but surpassed it in several critical areas, including weight reduction, stress management, and time efficiency.
Here’s a detailed look at how the two designs stack up:
Weight Reduction:
- First, Cognitive Design excelled at minimizing weight without compromising structural integrity, reducing part's volume to 23.5 cm³ compared to 30,5cm³ for the ULA GrabCAD challenge winner. This translated into an overall 13% reduction in weight (35,7g instead of 40,7g), which is a substantial achievement in the aerospace industry, where even minor weight savings can have a large impact on payload capacity and fuel efficiency.
Stress and Strength Metrics:
- The first-prize design achieved a maximum stress of 33 MPa, but Cognitive Design’s solution improved upon this, reducing the maximum stress to just 25 MPa. This 24% improvement in stress performance means that the optimized part not only handled the required loads but did so with a more efficient material distribution, further enhancing durability and reliability.
Time Savings:
- One of the standout advantages of using Cognitive Design was the dramatic reduction in design time. Traditional design methods, including those used by the first-place winner, took 50 hours to complete the design and optimization process. In contrast, Cognitive Design, utilizing automated workflows and advanced simulation-driven design tools, completed the entire process—including topology optimization, simulations, and design refinements—in just 4 hours. This represents a 92% reduction in design time, demonstrating how automation and advanced optimization tools can drastically accelerate engineering workflows while maintaining superior results.
Conclusion: A Promising Future for Design Optimization
The ULA Grabcad Challenge highlights the best in engineering innovation, and as this case study has demonstrated, there is always room for further optimization. Through the use of powerful optimization tools in Cognitive Design, we not only met but surpassed the performance metrics of the first-prize-winning solution by delivering a part that was lighter, stronger, and more cost-efficient to design. This case study prooves that Cognitive Design can revolutionize engineering workflows, dramatically reducing design time and labor costs without sacrificing quality.
This challenge is just one example of how automation and intelligent design can transform the way engineers address complex problems. Cognitive Design’s ability to push current methods, refine designs more quickly, and achieve superior results marks a new frontier in industrial part optimization.
Learn more about how Cognitive can support you in tackling your next engineering challenges here.
Interested in reading the full case study?
Fill in the form below to instantly receive the full case study.
Aeronautics Challenges We Address
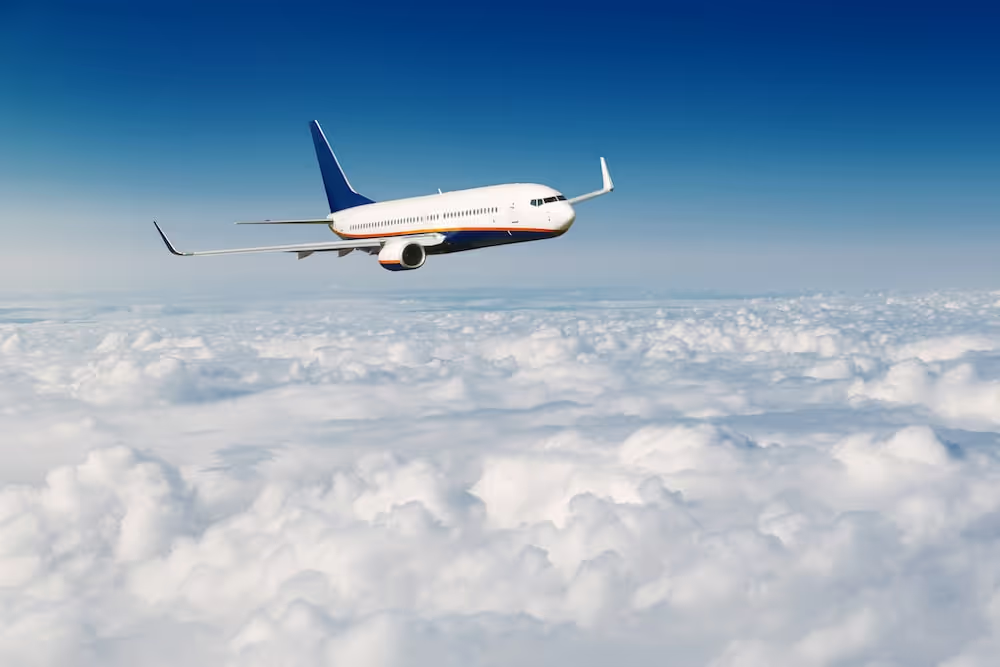
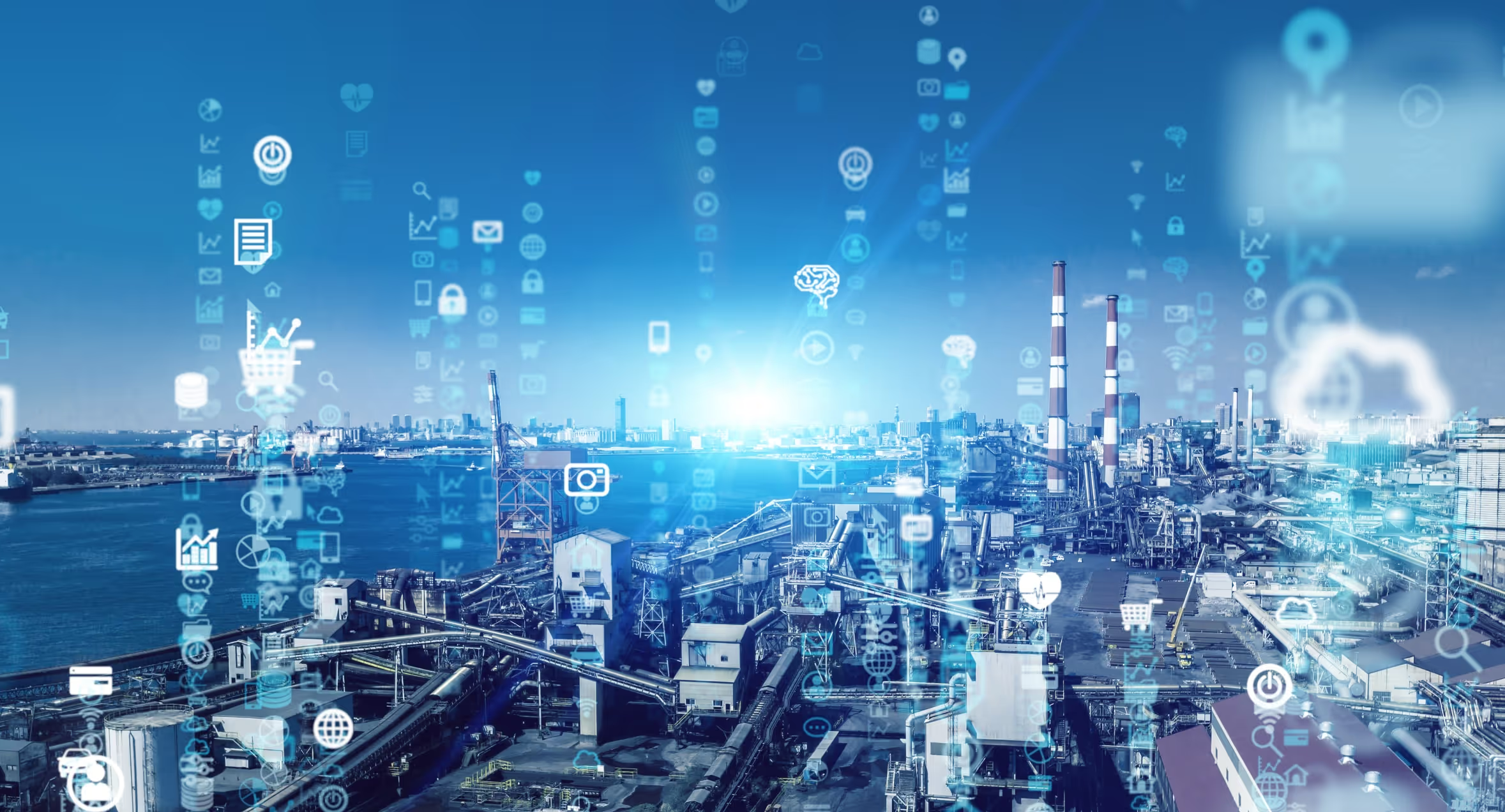
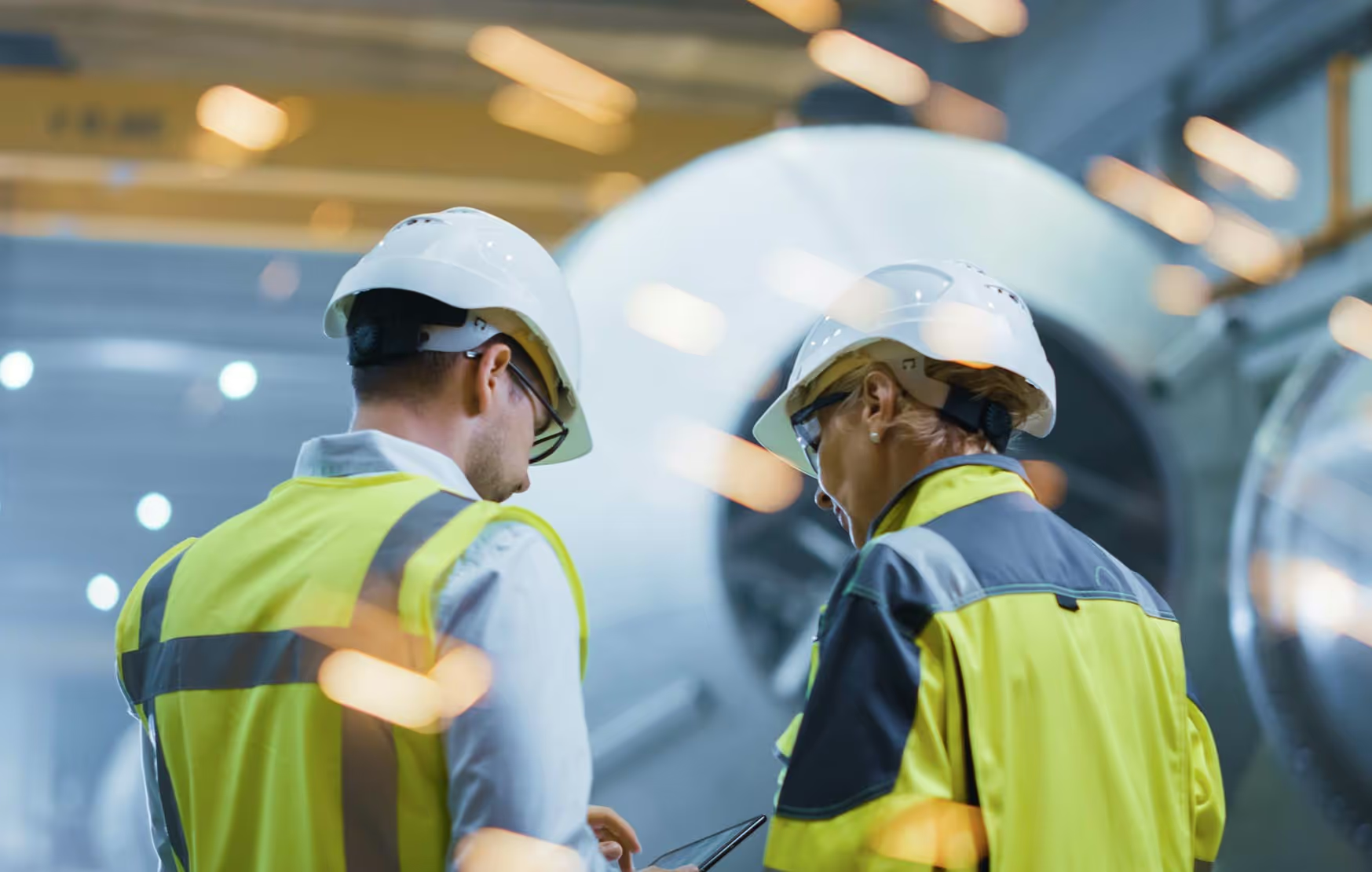
Automotive Challenges We Address
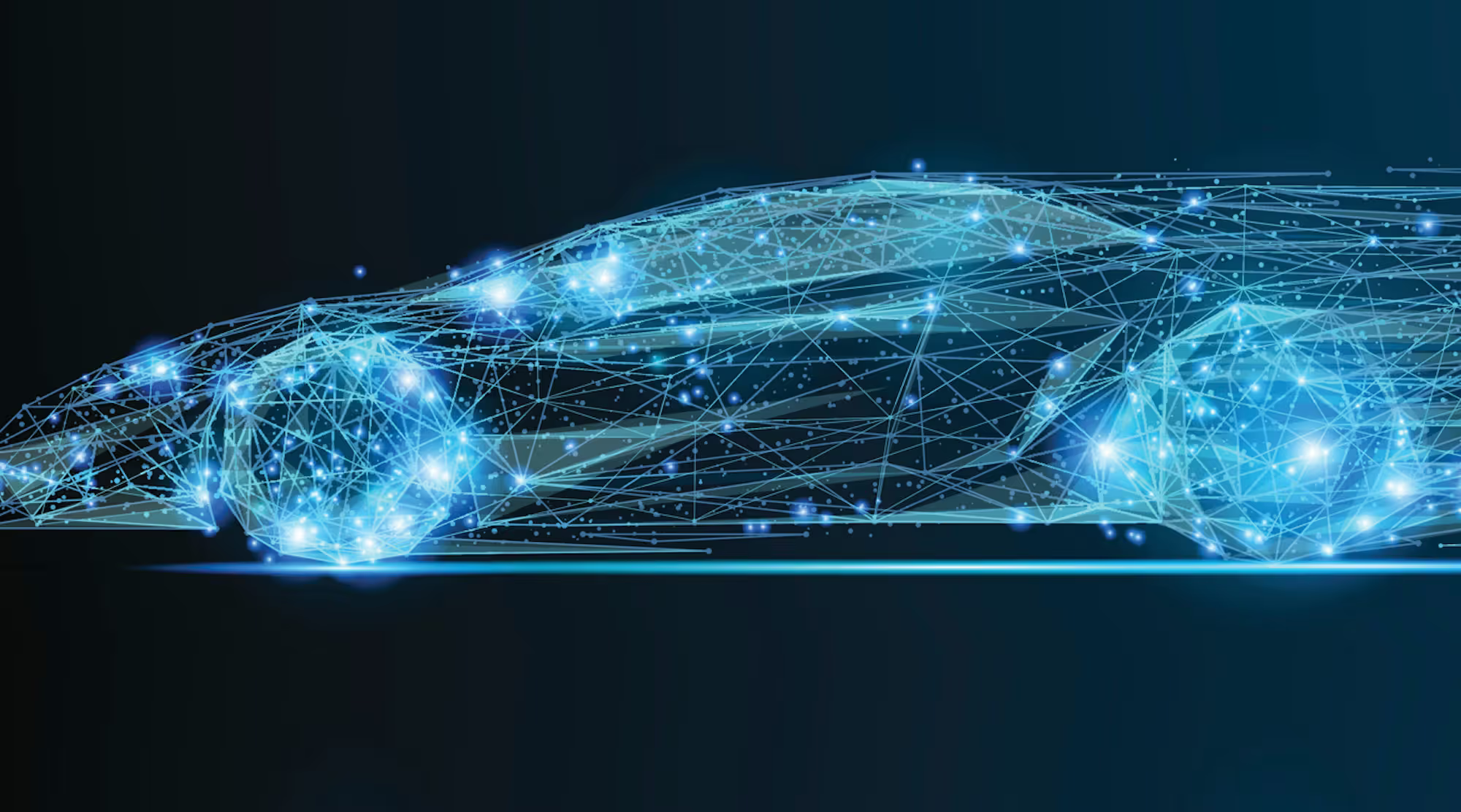
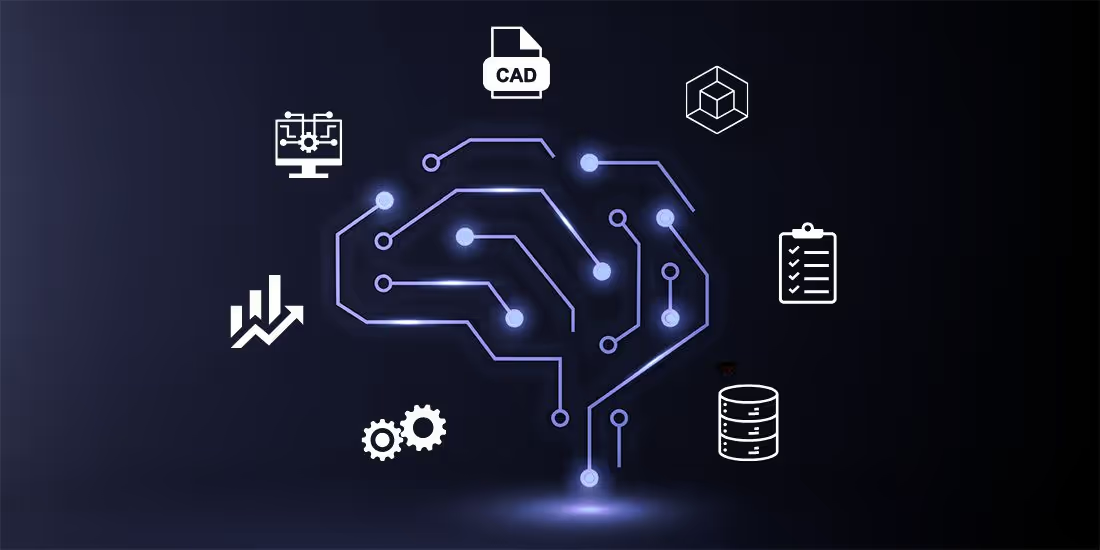
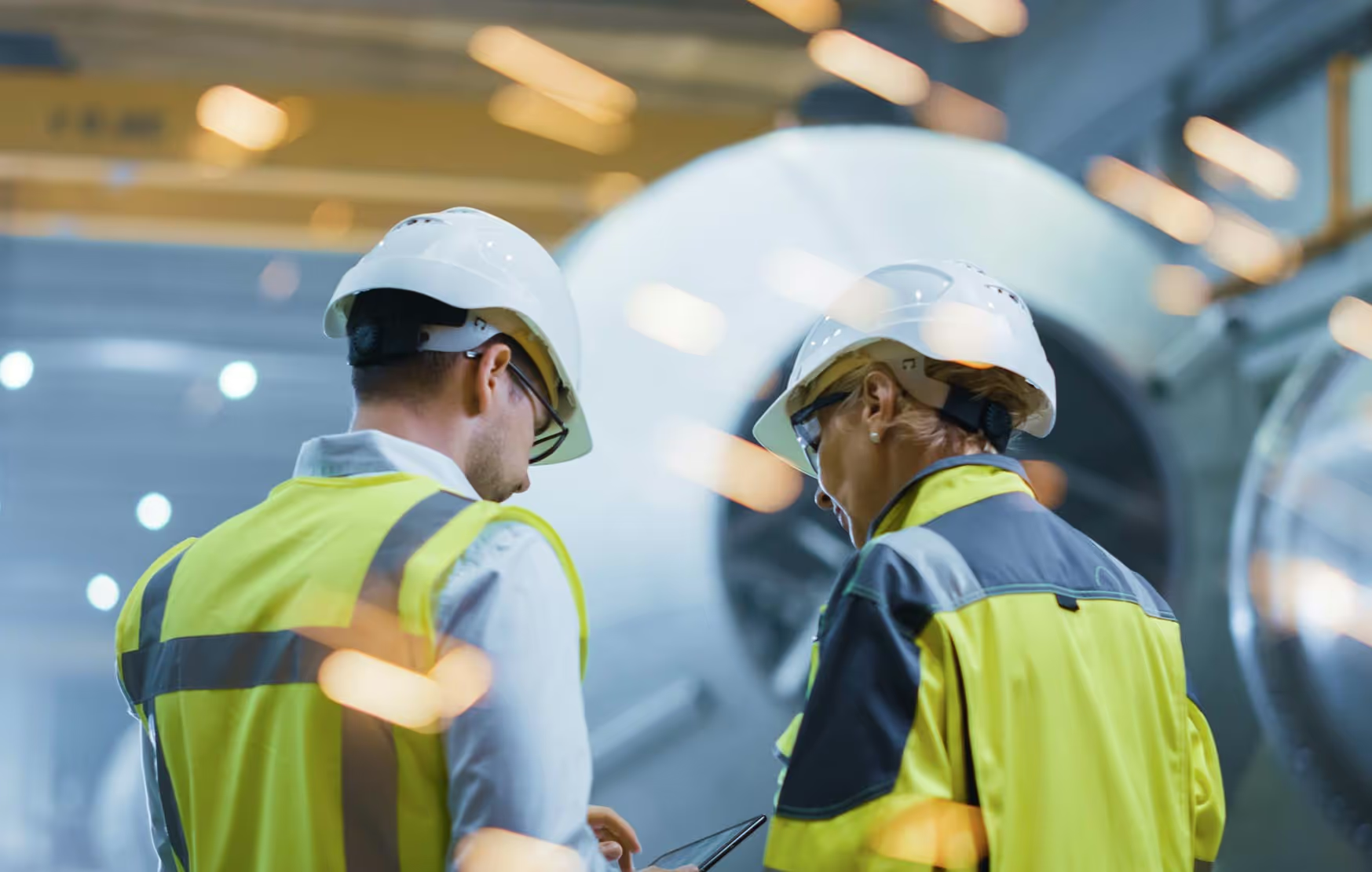
Defense Challenges We Address
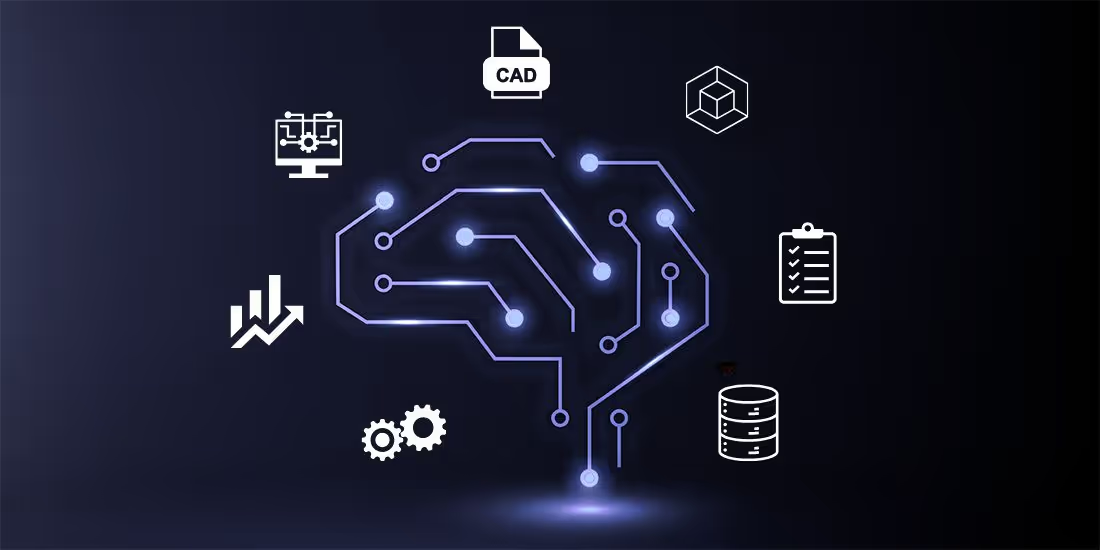
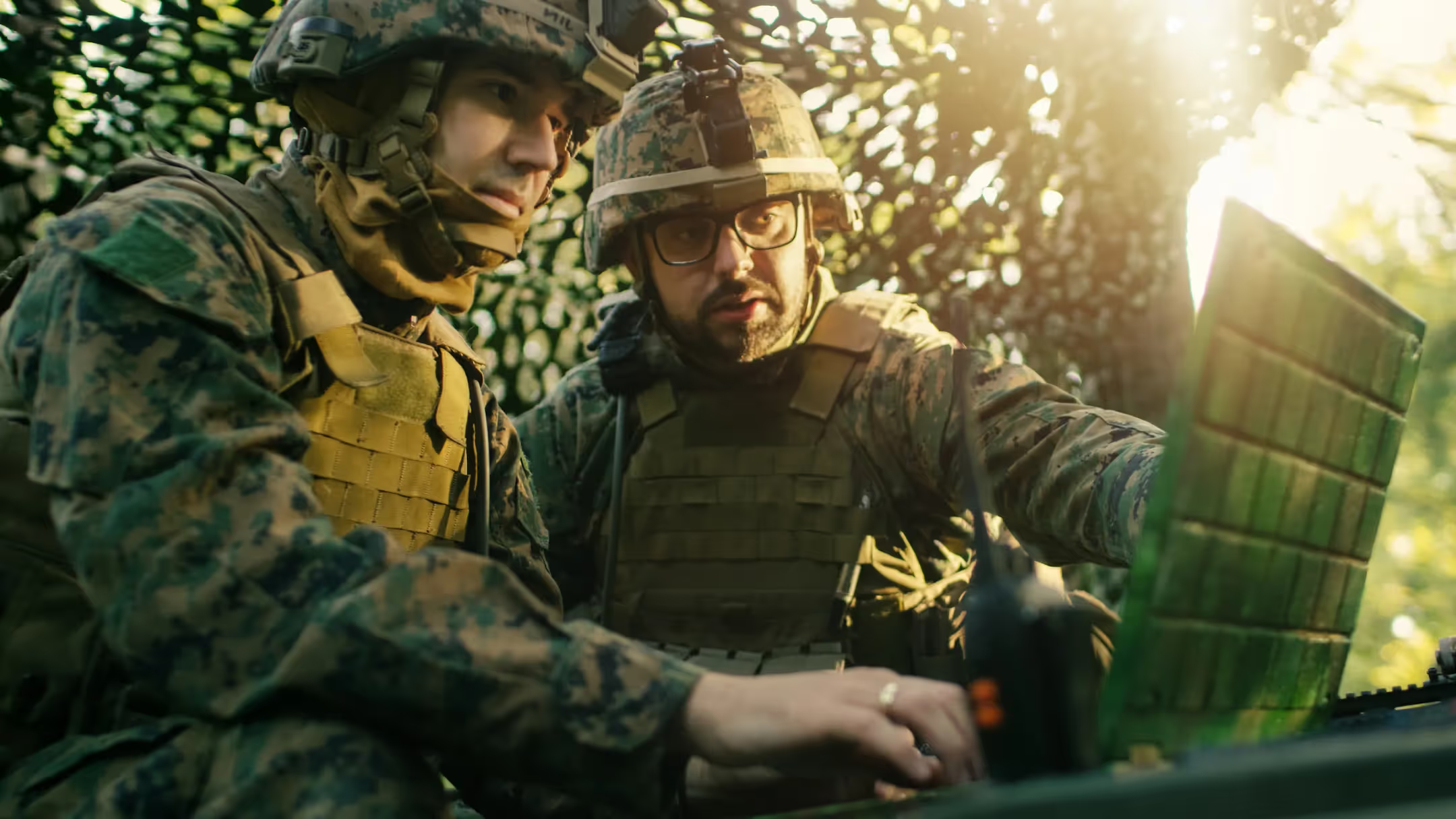
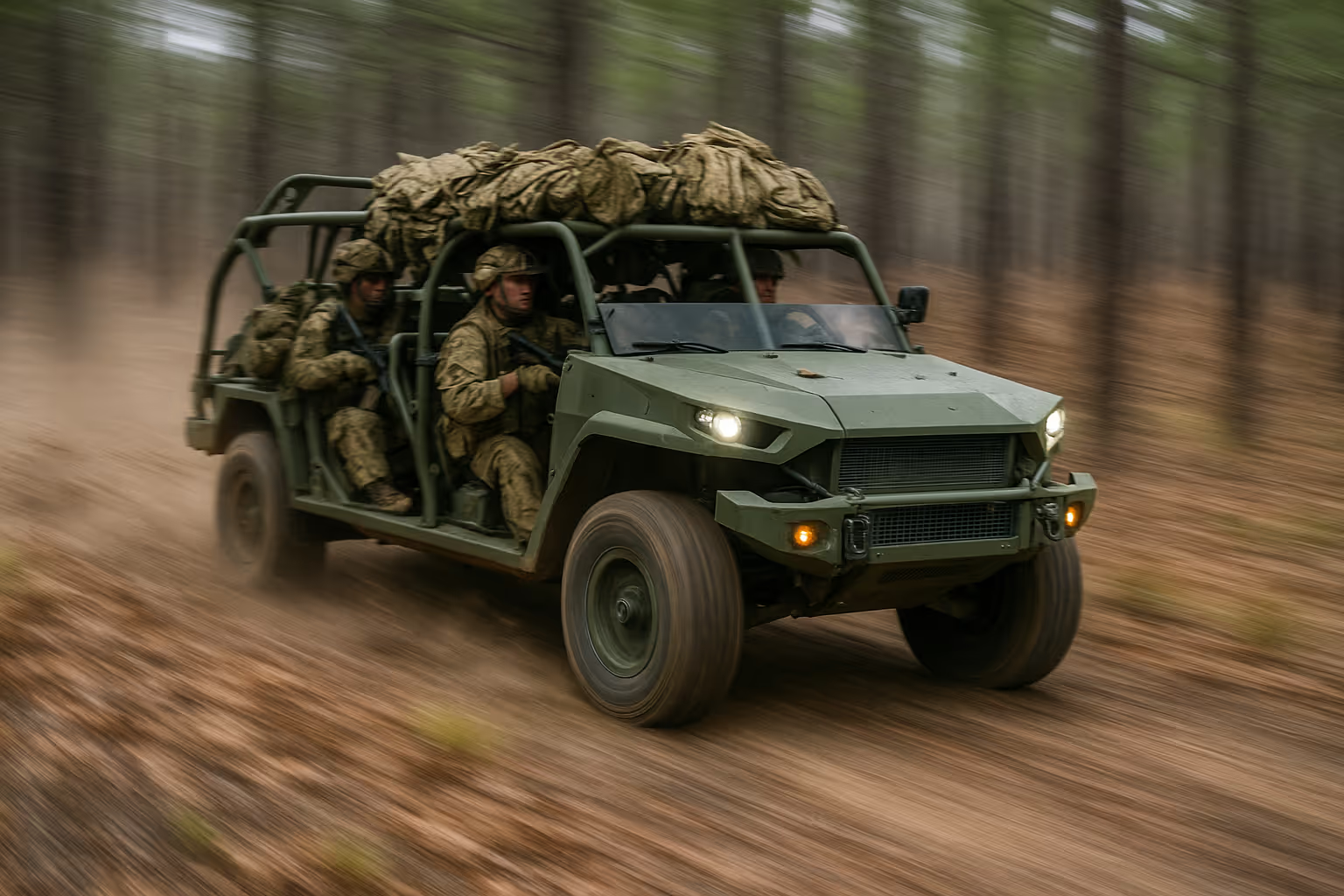
Built for the Cognitive Era of Engineering
Shorten product development cycle from the earliest concept phase.
Product engineering cycle
Product engineering cycle
Reusability of engineering workflows
FAQs
Explore our frequently asked questions to understand how our software can benefit you.
Yes, some functions in Cognitive Design by CDS use AI (costing, conversion to CAD, manufacturing analysis). It is pre-trained by CDS and packaged in the software, so there is no training happening on your side, and your data is not used.
Yes, you can convert mesh or implicit models to CAD and export them as a .step. It works best for midly complex models (e.g. generative design results). Complexe models (integrating lattice structures for instance) can also be converted to CAD, but would take more time..
No, our workflows use hybrid meshing, keeping the original CAD precision around functional regions, and having smooth mesh elements on organic features.
Cognitive Design by CDS uses a proprietary hybrid geometrical engine, mainly based on implicit modeling (Signed Distance functions), with in addition mesh and CAD operators.
Cognitive Design by CDS uses a node-locked license system, tied to each workstation. This approach aligns with the offline, on-premise setup. Floating licenses are not yet available.
Cognitive Design by CDS is particularly well suited for complex, high-value mechanical parts such as lightweight structures, gearbox housings, functional brackets, or fixtures subjected to multiphysics loads. It is optimized for use cases in aerospace, defense, space, and advanced mobility systems.
Cognitive Design by CDS is an advanced concurrent plaftorm for design optimization that enhances component performance. It incorporates production constraints directly into the design phase, ensuring efficiency. This allows design engineers to streamline workflows and reduce development time.
Cognitive Design by CDS is tailored for engineers in large and medium-sized industrial companies. It is particularly beneficial for sectors like aerospace, automotive, defense, and space. The software addresses unique engineering challenges faced in these industries.
Cognitive Design by CDS uses an implicit modeling engine and parametric design to generate and optimize designs rapidly. By factoring in manufacturing constraints, it ensures that designs are feasible and efficient. This process minimizes the risk of failure during production.
Cognitive Design by CDS significantly reduces development time and enhances agility in the design process. It allows for quick iterations and optimizations, keeping your projects on track. By integrating manufacturing constraints early, it helps maintain competitiveness.
While Cognitive Design by CDS is user-friendly, we offer comprehensive training to maximize its potential. Our support team is available to assist with onboarding and any questions. This ensures that users can leverage the software effectively.
Unlock Your Design Potential
Request a demo to see how Cognitive Design by CDS can revolutionize your engineering workflow